Started on the parachute deployment mechanism. Drilled and tapped the hole to take the actuator piston then worked out where it needed to pass through the body. Drilled a hole and then discovered an issue I thought I would have. The actuator fouls the fuel tank.
Two options. Move the tank or shorten the actuator. Moving the tank is the cheapest option but the most time consuming option as a new fuel line would have to be made. The other option is to reduce actuator length, which I knew I may have to do when I bought the 250mm long one. Going to 200mm will solve the clearance issue but reduce the force applied to the parachute. So I have increased the bore from 25mm to 32mm. This increases the volume of air moved by 31% so should apply more force to the parachute.
Next task was to work out how to mount the actuator to the parachute support as it wasn't designed for this task. I have decided to make a cup that fits over the hole in the support frame to hold the actuator. unfortunately, after making the mould and preparing the carbon and bagging materials I discovered that the last dregs of resin I had had started to solidify so that was binned and a 1Kg was ordered from Easy Composites which should be here by Friday.
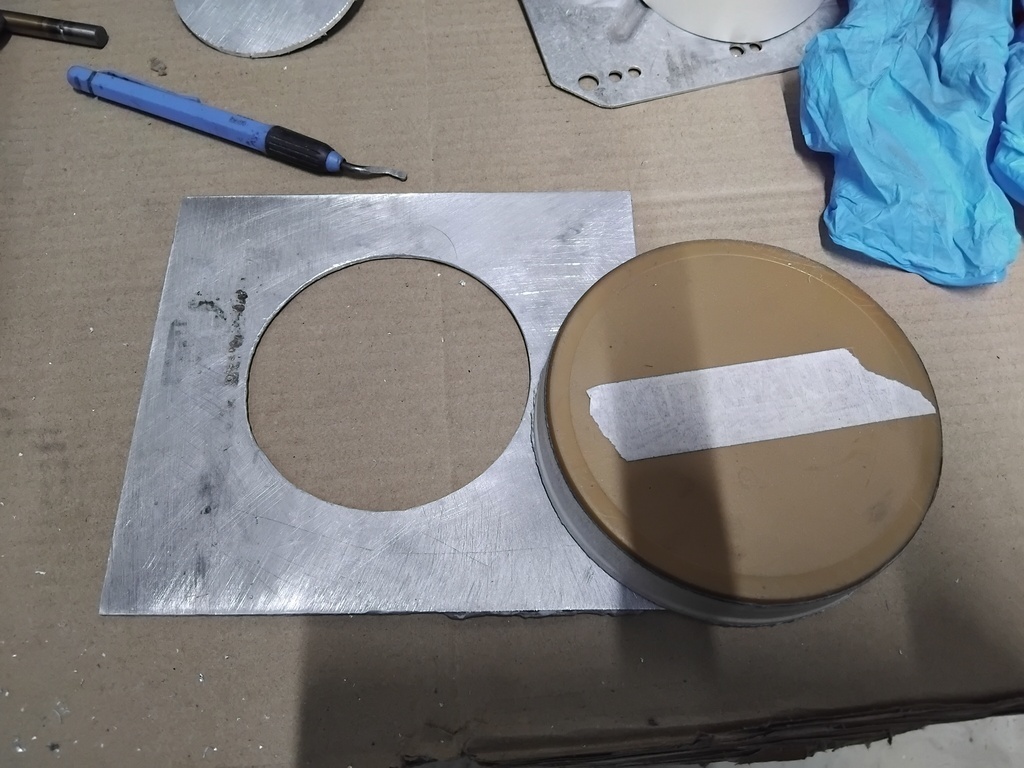
I had to order a new solenoid for the parachute release mechanism as the one I planned to use was a normally open version and I need a normally closed one.
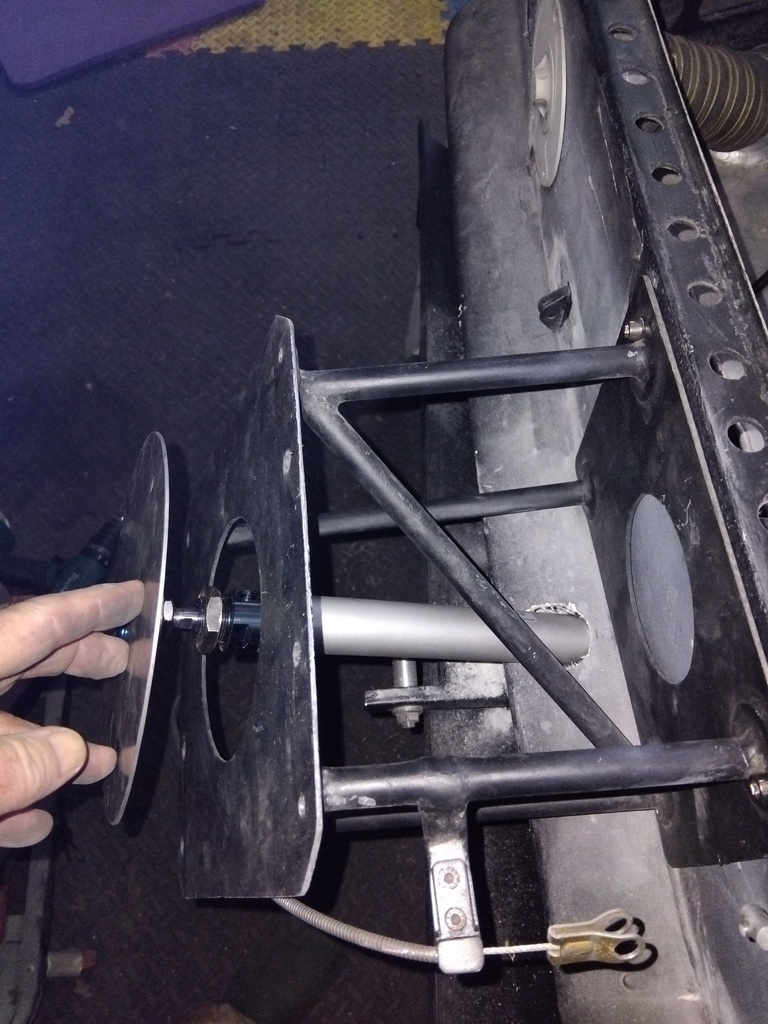
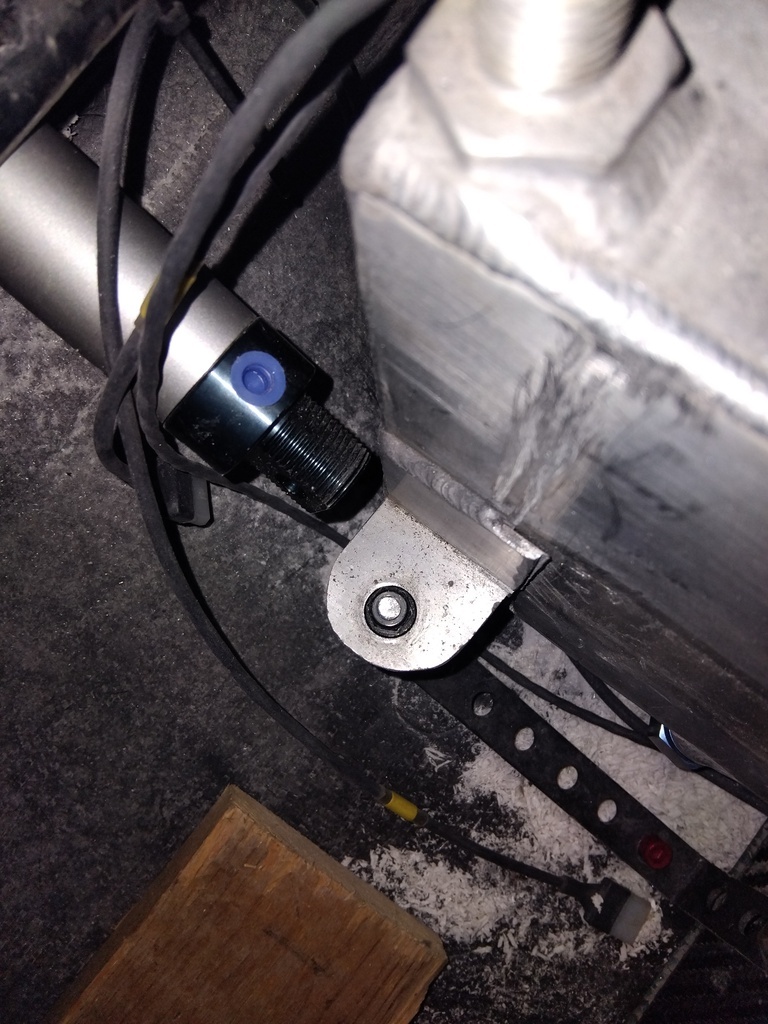
Two options. Move the tank or shorten the actuator. Moving the tank is the cheapest option but the most time consuming option as a new fuel line would have to be made. The other option is to reduce actuator length, which I knew I may have to do when I bought the 250mm long one. Going to 200mm will solve the clearance issue but reduce the force applied to the parachute. So I have increased the bore from 25mm to 32mm. This increases the volume of air moved by 31% so should apply more force to the parachute.
Next task was to work out how to mount the actuator to the parachute support as it wasn't designed for this task. I have decided to make a cup that fits over the hole in the support frame to hold the actuator. unfortunately, after making the mould and preparing the carbon and bagging materials I discovered that the last dregs of resin I had had started to solidify so that was binned and a 1Kg was ordered from Easy Composites which should be here by Friday.
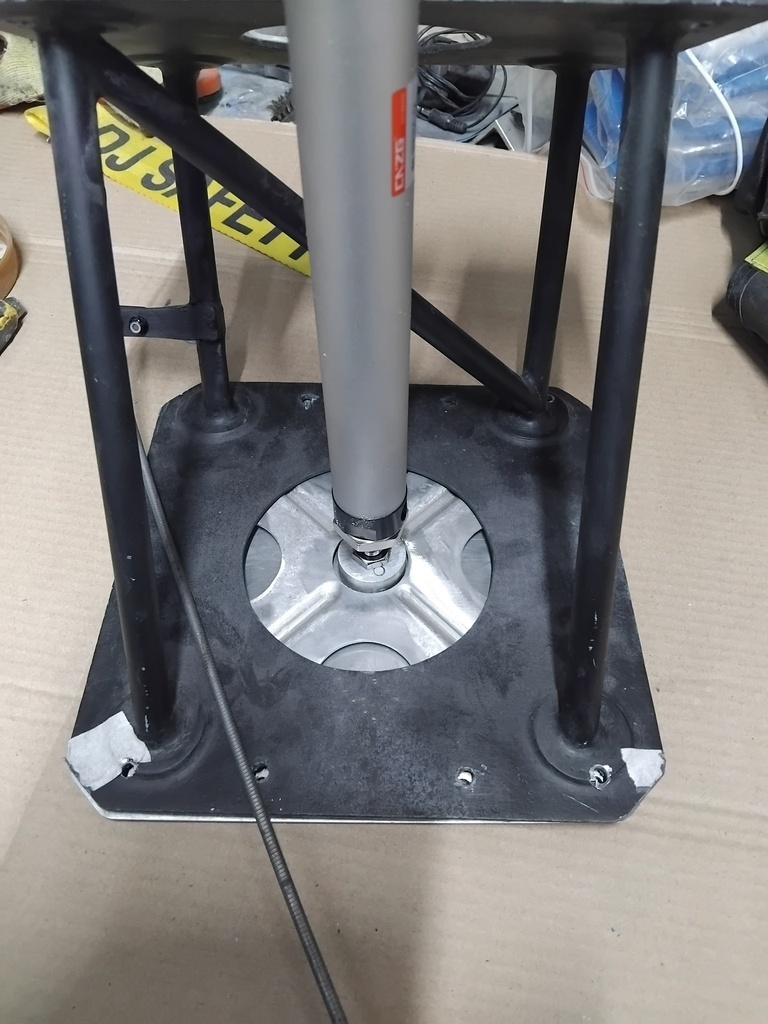
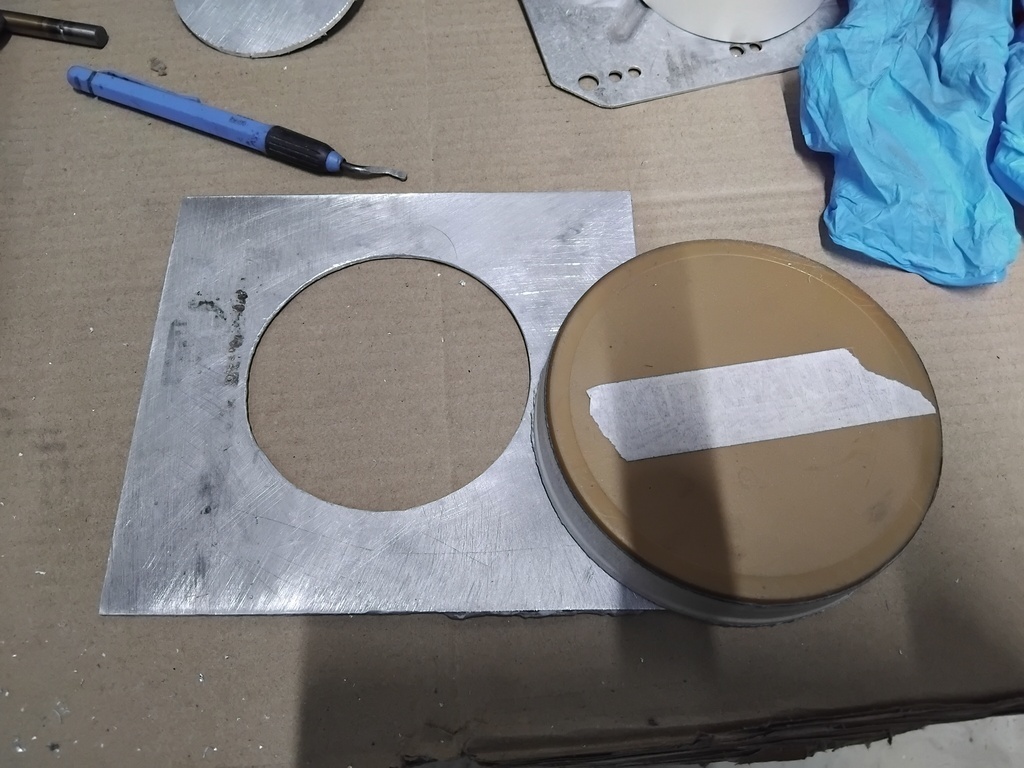
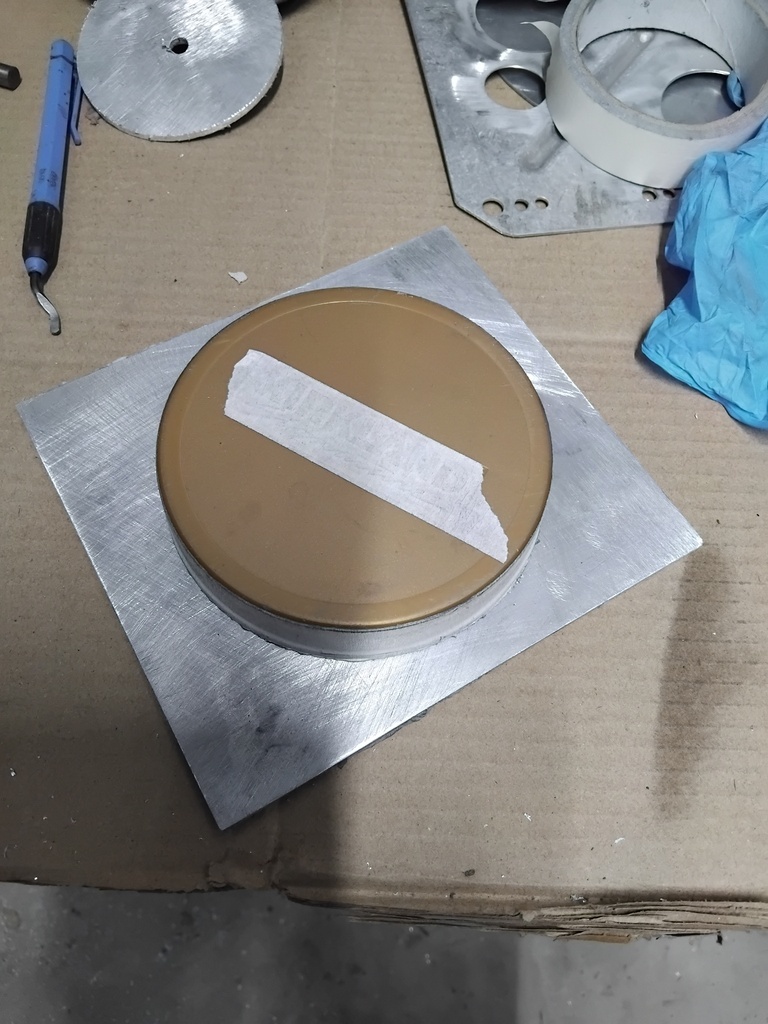
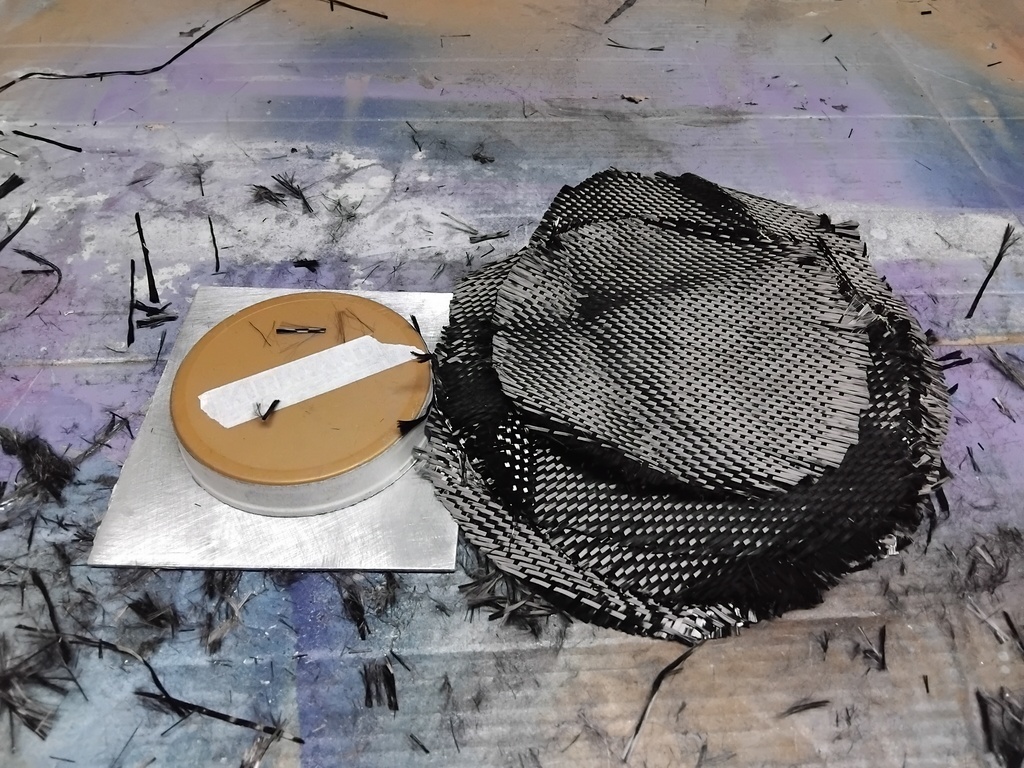
I had to order a new solenoid for the parachute release mechanism as the one I planned to use was a normally open version and I need a normally closed one.