|
|
|
I know it’s nowhere near finished, as you quite rightly say, but for us readers it’s really taking shape. I’ve thoroughly enjoyed this thread so far and just want to say thanks again for taking the time to post about it 👍 That's really kind of you, thank you but it is a two way thing because I derive a lot of energy from your continuing support and encouragement as well as profiting from carefully considered suggestions. Sometimes it is all too easy to be standing too close and not seeing the bigger picture which is why it is always good to receive input from others who are not so closely involved in the project as I am. I've got a little open day lined up for the weekend so I'm trying to spruce things up a bit resulting in no actual work being done and next week when I resume, I shan't be able to find anything doh! I'm sure we have all been there. It may be a mess but I know where everything is, or I did.
|
|
|
|
|
|
|
Aug 16, 2024 12:23:30 GMT
|
|
|
|
|
|
|
|
It's been a while since my last offering but there really hasn't been much to detain you. I made an error way back with the rear quarters and I'm now in the middle of rectifying the problem. I'm referring to the profile of the wing as it curves down to meet the sill at the B post. I'm sure I had a good reason for doin it this way but it's such a long time ago that I have forgotten why. All I do know is that it is clearly wrong and has to be altered so that the line follows through from the front to the back. It is always a bit daunting having to go back and unpick work but there is no alternative and I have had to bite the bullet. I took a cutting disc to separate it from the B post. 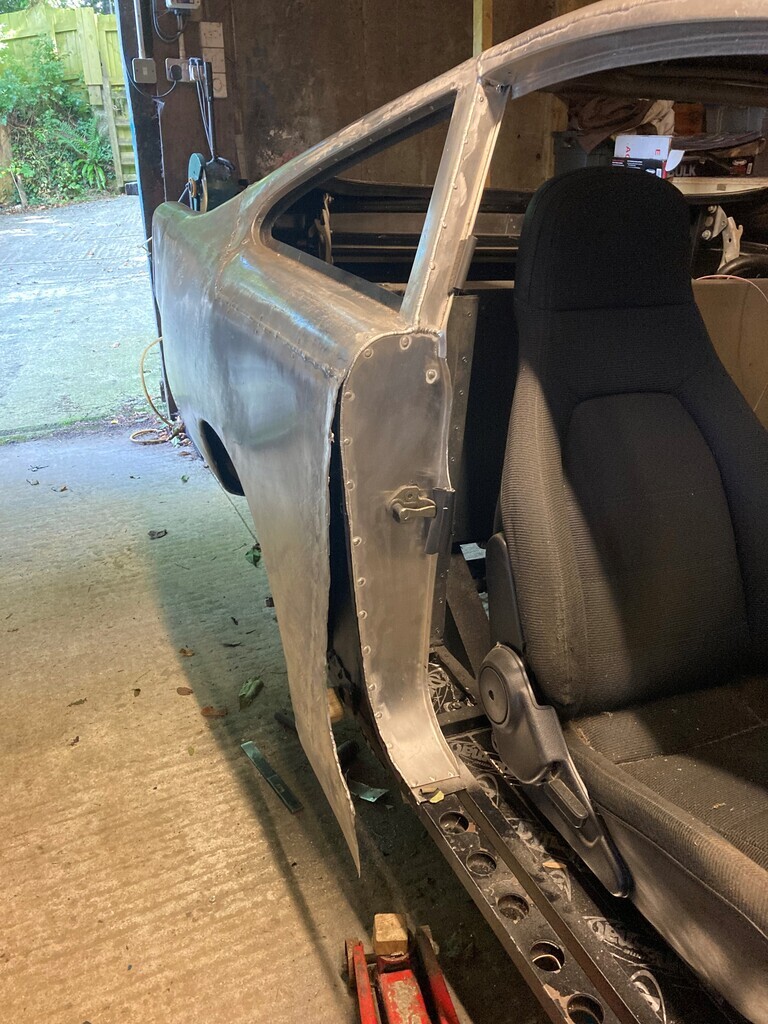 The sill needed to be extended outwards Before reshaping the wing I began making a door frame to ensure the profile follows through. The door frames are being fabricated from 5/16" ERW which is easy to work with, certainly easier than 2mm aluminium of 16swg steel sheet and should when complete be robust.The joiners between the hinges and the tube were interesting pieces to make.Starting material was 2" x 1" ERW box section, one face removed to weld in a captive nut and then weld the top back on. It was a nice moment when the door hinged open and closed.Everything just tacked up for the moment. A gusset and a bit of triangulation added. So there we are, up to date once more. Thank you for reading and your support.
|
|
|
|
mk2cossie
Club Retro Rides Member
Posts: 3,063
Club RR Member Number: 77
|
|
|
As others have said, none of this build is boring to us readers. We are all always as happy for little updates as big ones  And even though you've taken to the rear quarter, that looks to me like good progress 
|
|
|
|
|
|
|
Fantastic as ever. I love seeing your work
|
|
|
|
skinnylew
Club Retro Rides Member
Posts: 5,719
Club RR Member Number: 11
|
|
|
 wow that's mega impressiv work indeed!
|
|
|
|
|
|
|
Can anyone please let me know what the plastic fitting is called and even better, where I can source them from? The picture is of a MK4 Fiesta door latch. Thank you John
|
|
|
|
|
|
|
|
Great thought, thank you.
I hope you are well
Best wishes
John
|
|
|
|
|
|
|
I'm doing good, John, thank you. Hope you are as well 
|
|
|
|
|
|
|
|
You may remember that I made a big mistake with the profile of the rear quarter panels and today I made up my mind to to do my best to rectify it. I had already slit the panel and pulled it out to the new extended sill supporting frame so that was a start I cut out the aluminium B post piece and cleaned up the hacked about panel. Next I folded a 40mm wide length of aluminium into a 20 x 20mm right angle section and using the shrinker/stretcher reproduced the profile to match the door frame. Using a plywood former the panel was coaxed into taking up the shape I wanted The shaped angle was then slipped into its temporary position. Eyeing the car down its length I think it looks okay now.
|
|
|
|
gazzam
Part of things

Posts: 746
|
|
|
Glad you found a reasonably easy fix and pleased that you’re making progress. All the best.
|
|
|
|
|
|
|
Glad you found a reasonably easy fix and pleased that you’re making progress. All the best. Good to hear from you, thank you. The most difficult part is always avoiding the temptation to compound the error by carrying on, building on the mistake and making the difficult decision to either start again or unpick the problem. Once that's done the hardest part's over and with it comes the elation that the the job is right and that there is nothing that's going to bite you farther down the line. I'm sure we have all been in this position and can relate to the situation.
|
|
|
|
|
|
Oct 17, 2024 18:15:41 GMT
|
A little bit of progress that I can share with you. I'm using the door latch and lock from the donor Fiesta and needed to fashion a housing to accommodate it. My first thought was to hammerform it from sheet steel but then decided upon the easier option of fabrication. I started with a length of 50mm x 25mm x 1.5mm ERW box section split down its length into a L section.I needed a width of 95mm so I welded two of the L sections longitudinally to provide a front and two sides of the box. The tabs at each end were folded to a right angle to finish the box.The enclosure was then welded to a piece of 18 gauge steel which goes across the width of the door. Once welded, the upstands were sanded flush and the latch mechanism fitted And finally, just to show that it works
|
|
|
|
jimi
Club Retro Rides Member
Posts: 2,239
|
|
Oct 17, 2024 19:06:42 GMT
|
Nice, once the door is skinned and paneled it'll have a nice clunk when it closes 
|
|
Last Edit: Oct 18, 2024 23:25:41 GMT by jimi
Black is not a colour ! .... Its the absence of colour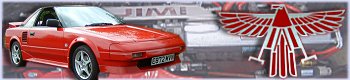
|
|
jimi
Club Retro Rides Member
Posts: 2,239
|
|
Oct 18, 2024 23:30:32 GMT
|
|
|
Black is not a colour ! .... Its the absence of colour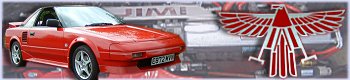
|
|
|
|
Oct 22, 2024 12:39:51 GMT
|
Using a length of folded 18 gauge sheet steel I shrunk it to match the profile of the outer tube and tacked it in place using the transverse square tube distance pieces to locate it. This has now given the door another dimension and added stiffness. Everything is still only tacked in place waiting for me to pluck up the courage to commit and fully weld it.
|
|
|
|
|
|
Oct 23, 2024 17:56:23 GMT
|
|
|
|
|
|
|
Oct 24, 2024 12:46:15 GMT
|
The next little conundrum is to decide on framed or frameless windows. In any event there will need to be fixed, framed quarter lights to allow room in the door for the glass when the window is down but I'm currently favouring frameless similar to the GT6. Woolies supply aluminium channel for the glass but it's only 1.5mm wall so it could be quite flimsy. I do have a short length of 2mm wall channel so I know that is available and would definitely be stiff enough but it would need to be formed to match the roof curve and the top rail demountable to insert the glass, none of which would be necessary were there no frames. Do you know, I've just talked myself into making the decision  Frameless it is. Having had a couple of GT6s I can vouch for how fiddly a job it is fitting the retaining clips for the outer glass weather seals so I'm hoping to design out that little feature. I'm thinking about making the inner door lining to which the internal door handles and the electric lifters will be attached removable which, if possible, will help the cause no end by increasing accessibility . There are pros and cons to scratch building and I would suggest that a major plus point of a self-build is being able to take into account future maintenance and problems by building in accessibility, something which is very often found wanting on mainstream vehicles. I'm sure we can all cite our own examples and the frustration of having to spend far longer than should be necessary to do a simple job. I've never understood why this is so because one would have thought that on a production line where every second counts, why not design in ease of assembly. Case in point, fitting the window winder handle to a GT6 where a spring, escutcheon plate and the handle have to held in just the right position for a pin to be dropped into the shank. The obvious answer, screw on the handle which is what I did on my GT6 and save time. Just an example but I can think of many more as I'm sure can you. Anyway, back to the door which is actually quite a complex component where just about everything is interdependent and needs to be fully integrated to avoid clashes and to operate correctly. I'm finding it challenging this being the first door I have made but it is, nonetheless, a very interesting and absorbing sub-project. I'll keep you posted and thank you for reading and your support.
|
|
|
|